Efektywne zarządzanie magazynem to podstawa sprawnej logistyki. Błędy w organizacji mogą prowadzić do zwiększonych kosztów, błędów w inwentaryzacji i opóźnień w realizacji zamówień. W tym wpisie przedstawiamy 10 najczęstszych błędów w magazynach i sposoby na ich eliminację.
1. Nieefektywne wykorzystanie przestrzeni magazynowej
Brak przemyślanej organizacji przestrzeni prowadzi do strat i spowolnienia pracy.
- Zbyt szerokie alejki ograniczają miejsce składowania,
- Towary rozmieszczone losowo wydłużają kompletację zamówień,
- Brak strefowania produktów utrudnia organizację.
Rozwiązanie:
- Analiza ABC – produkty o wysokiej rotacji umieszczone w łatwo dostępnych miejscach,
- Regały wysokiego składowania – lepsze wykorzystanie przestrzeni.
- Optymalizacja układu magazynu zgodnie z zasadami Lean Logistics.
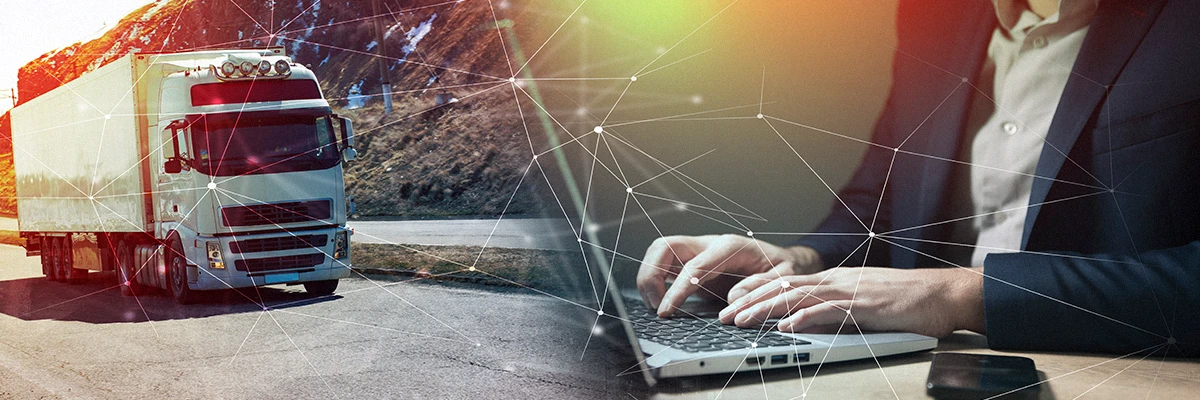
2. Brak systemu WMS (Warehouse Management System)
Wiele firm nadal korzysta z Excela lub ręcznych zapisów, co prowadzi do rozbieżności w stanach magazynowych i błędów w realizacji zamówień.
Rozwiązanie:
- Wdrożenie systemu WMS – automatyczna kontrola zapasów i lepsza organizacja procesów
- Integracja WMS z ERP – synchronizacja stanów magazynowych i sprzedaży
3. Brak regularnej inwentaryzacji magazynu
- Brak cyklicznej kontroli powoduje błędy w stanach magazynowych
- Przestarzałe metody ręcznego liczenia zwiększają ryzyko strat
Jak to poprawić?
- Inwentaryzacja cykliczna zamiast rocznej
- Automatyczne skanowanie RFID lub kodów kreskowych
- Podwójna weryfikacja w przypadku drogich produktów
4. Nieprawidłowe etykietowanie towarów
Nieczytelne lub brakujące oznaczenia powodują zamieszanie i błędy w wysyłkach.
Rozwiązanie:
- Kod kreskowy lub RFID dla każdego produktu
- Czytelne oznaczenia lokalizacji na regałach
- Automatyczne skanowanie produktów przy każdej zmianie lokalizacji
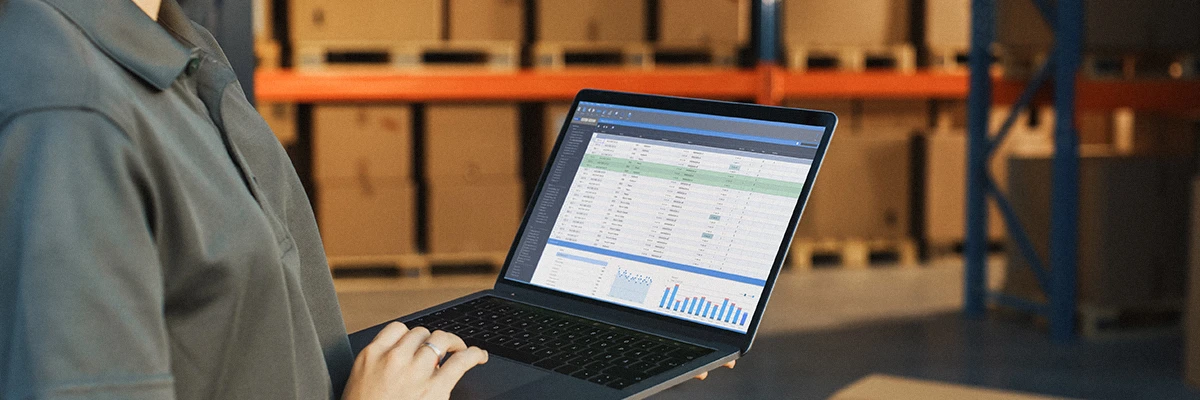
5. Brak optymalizacji procesu kompletacji zamówień
Źle zorganizowana kompletacja zamówień wydłuża czas realizacji i zwiększa błędy.
Jak to poprawić?
- Batch Picking – zbiorcza kompletacja kilku zamówień
- Zone Picking – podział magazynu na strefy kompletacyjne
- Pick-to-Light i Pick-by-Voice – eliminacja błędów ludzkich
6. Nieoptymalne ścieżki przepływu towarów
Złe planowanie tras magazynierów prowadzi do niepotrzebnych strat czasu.
Jak to poprawić?
- Analiza tras kompletacji i reorganizacja stref
- Dynamiczne składowanie według częstotliwości pobrań
- Skrócenie dystansu między strefami magazynu
7. Nieprzemyślana organizacja przyjęć i wysyłek
- Brak oddzielenia stref przyjęć od kompletacji
- Opóźnienia w księgowaniu dostaw
- Błędy w wysyłkach
Jak to poprawić?
- Automatyczne skanowanie przyjętych towarów
- System etykietowania i sortowania paczek
- Integracja WMS z firmami kurierskimi
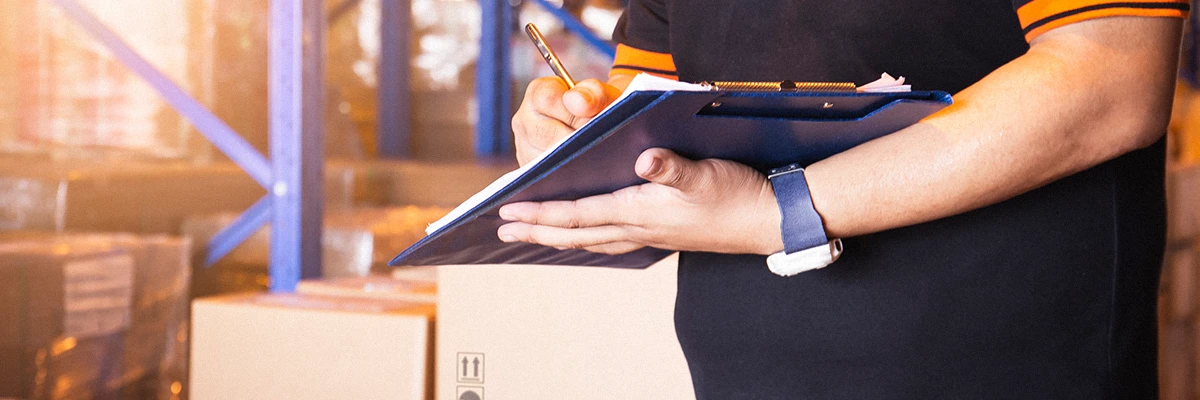
8. Nieprawidłowe zarządzanie zapasami magazynowymi
Zbyt duże zapasy generują koszty, a ich brak powoduje opóźnienia w realizacji zamówień.
Jak to zoptymalizować?
- Metoda ABC – klasyfikacja produktów według rotacji
- Just in Time (JIT) – składowanie tylko niezbędnych towarów
- Monitorowanie wskaźnika OTIF (On Time In Full)
9. Brak szkoleń pracowników magazynowych
Bez przeszkolenia magazynierów nawet najlepszy system WMS nie będzie działał efektywnie
Jak temu zaradzić?
- Regularne szkolenia z obsługi systemu WMS
- Testy i symulacje awaryjne
- Programy motywacyjne dla pracowników
10. Brak analizy danych magazynowych
Firmy, które nie analizują wskaźników magazynowych, podejmują błędne decyzje operacyjne.
Co warto monitorować?
- OTIF (On Time In Full) – terminowość realizacji zamówień
- FIFO / LIFO – rotacja zapasów
- Średni czas realizacji zamówienia
- Wskaźnik błędów kompletacji
Wdrożenie systemu BI (Business Intelligence) pozwala na automatyczne monitorowanie danych i optymalizację procesów.
Podsumowanie
Uniknięcie tych 10 błędów w zarządzaniu magazynem pozwala zwiększyć efektywność, ograniczyć koszty i poprawić obsługę klientów. System WMS, automatyzacja procesów i analiza danych to klucz do sprawnego magazynu.
Czy Twoja firma boryka się z tymi problemami? Skontaktuj się z nami i dowiedz się, jak możemy Ci pomóc wdrożyć skuteczne rozwiązania!