Effective warehouse management is the foundation of efficient logistics. Organizational errors can lead to increased costs, inventory errors, and delays in order fulfillment. In this post, we present the 10 most common errors in warehouses and ways to eliminate them.
1. Inefficient use of storage space
Lack of thoughtful organization of space leads to losses and slowdowns in work.
- Too wide aisles limit storage space,
- Randomly arranged goods prolong order completion,
- Lack of product zoning makes organization difficult.
Solution:
- ABC analysis – high-turnover products placed in easily accessible locations,
- High-bay racks – better use of space.
- Optimization of warehouse layout in accordance with Lean Logistics principles.
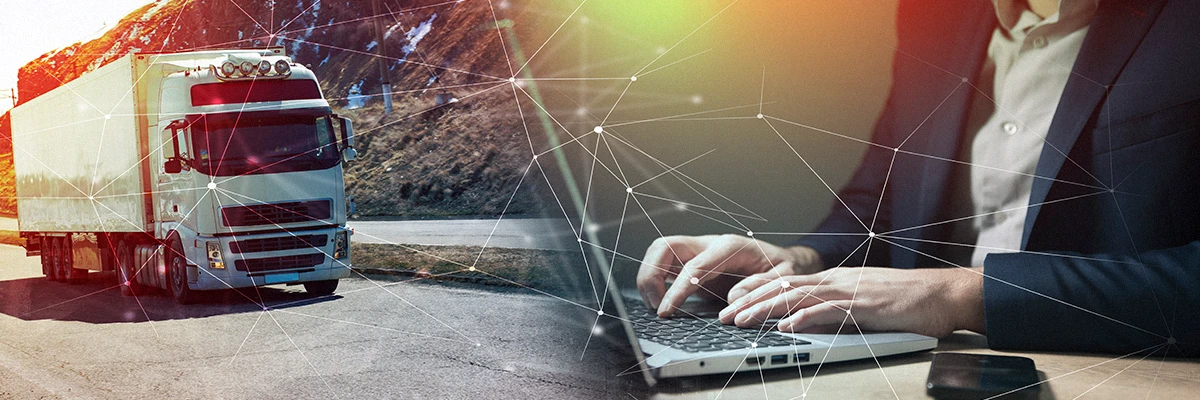
2. Lack of WMS (Warehouse Management System)
Many companies still use Excel or manual records, which leads to discrepancies in inventory levels and errors in order fulfillment.
Solution:
- Implementation of WMS system - automatic inventory control and better organization of processes
- Integration of WMS with ERP - synchronization of inventory levels and sales
3. Lack of regular inventory of the warehouse
- Lack of cyclical control causes errors in stock levels
- Outdated methods of manual counting increase the risk of losses
How to improve it?
- Cycle inventory instead of annual
- Automatic RFID or barcode scanning
- Double verification for expensive products
4. Incorrect labeling of goods
Illegible or missing markings cause confusion and shipping errors.
Solution:
- Barcode or RFID for each product
- Clear location markings on shelves
- Automatic product scanning at each change of location
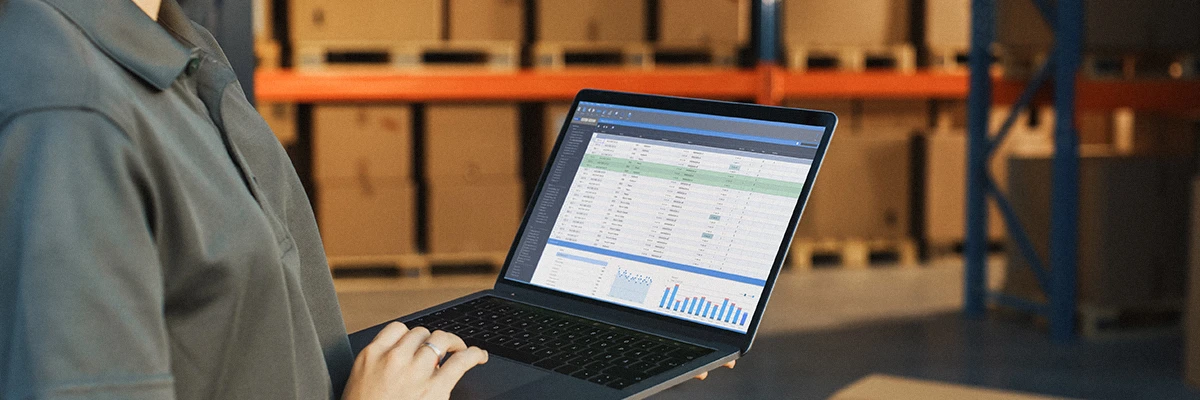
5. Lack of optimization in the order picking process
Poorly organized order picking extends lead times and increases errors.
How to fix it?
- Batch Picking – collective picking of multiple orders
- Zone Picking – dividing the warehouse into picking zones
- Pick-to-Light and Pick-by-Voice – elimination of human errors
6. Suboptimal goods flow paths
Poor planning of warehouse routes leads to unnecessary time losses.
How to fix it?
- Analyze picking routes and reorganize zones
- Dynamic storage based on picking frequency
- Reduce the distance between warehouse zones
7. Ill-considered organization of receiving and shipping
- Lack of separation between receiving and picking areas
- Delays in posting deliveries
- Shipping errors
How to fix it?
- Automatic scanning of received goods
- Package labeling and sorting system
- WMS integration with courier companies
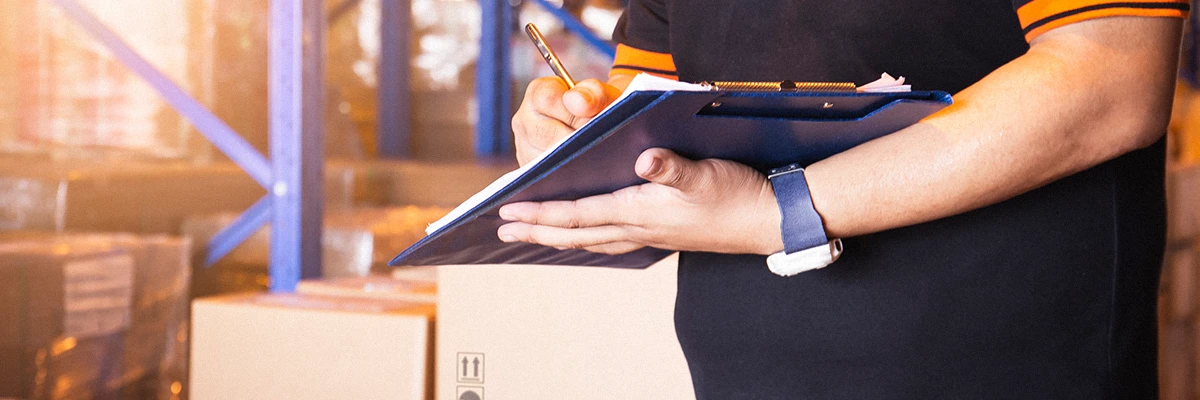
8. Improper warehouse inventory management
Excessive stock generates costs, while lack of it causes order fulfillment delays.
How to optimize it?
- ABC Method – classifying products by turnover
- Just in Time (JIT) – storing only necessary goods
- Monitoring the OTIF (On Time In Full) indicator
9. Lack of warehouse staff training
Without training for warehouse workers, even the best WMS won't operate efficiently
How to address it?
- Regular training on operating the WMS
- Emergency tests and simulations
- Employee incentive programs
10. Lack of warehouse data analysis
Companies that do not analyze warehouse metrics make misguided operational decisions.
What is worth monitoring?
- OTIF (On Time In Full) – on-time order fulfillment
- FIFO / LIFO – stock rotation
- Average order fulfillment time
- Picking error rate
Implementing a BI (Business Intelligence) system allows for automatic data monitoring and process optimization.
Summary
Avoiding these 10 warehouse management mistakes increases efficiency, reduces costs, and improves customer service. System WMS, process automation, and data analysis are key to an efficient warehouse.
Is your company struggling with these issues? Contact us to find out how we can help you implement effective solutions!