Multipicking with Weaver WMS - optimal work of the warehouse worker.
Multipicking in a warehouse is a technique of picking multiple orders at the same time on a single route through the warehouse, instead of picking each order separately. It is a process used primarily in logistics to increase the efficiency of warehouse operations and reduce order fulfillment times. In multipicking, a warehouse worker picks products for several orders at the same time, which minimizes the amount of movement around the warehouse and speeds up the entire order picking process.
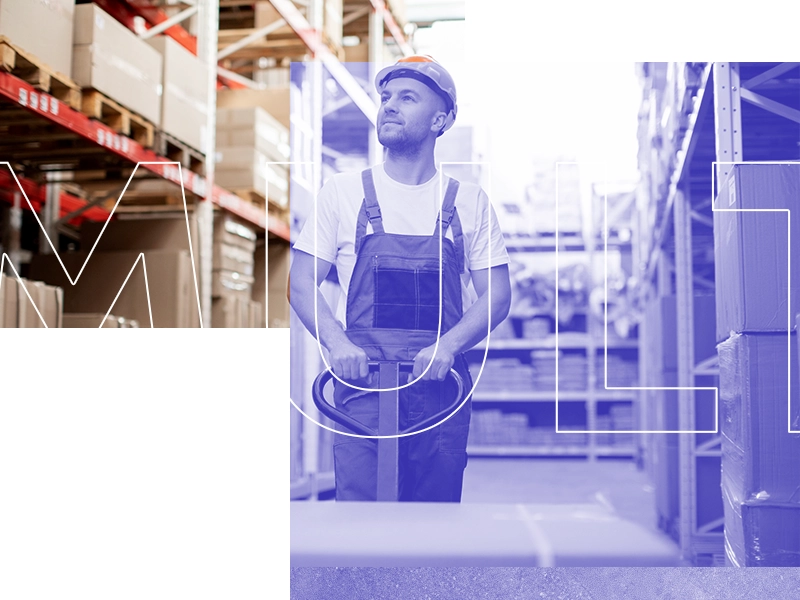
How does it work?
Grouping orders
Orders are grouped based on various criteria, such as the location of products in the warehouse, weight, size, or type of product. This allows a warehouse worker to collect products for several orders at once, moving through specific warehouse zones.
Choosing the right routes
A warehouse management system (WMS) optimizes employee routes to travel the shortest distance between product locations, minimizing travel time.
Collecting products
The warehouse worker collects products for all orders on one route, placing them in separate containers or on pallets, appropriately marked for different orders.
Final assembly
Once the route is complete, the products are delivered to the packing area where they are separated into individual orders and prepared for shipment.
Description of operation in the Weaver WMS system
Multipicking in our WMS system is based on:
Positions
Items are goods that the warehouse worker must pick according to the customer order. Each item has assigned information such as location in the warehouse, quantity, and picking priority. The WMS system dynamically assigns items to courses, optimizing the picking route.
Containers
Bins are storage units that receive the products collected during multipicking. Depending on the chosen picking strategy, bins can contain items from one or multiple orders. Proper bin management helps avoid packaging errors and speeds up the shipping process.
Mixed Strategy
In the Mixed strategy, one container can contain different products, but only from one order. This solution allows for more flexible management of space in containers and optimization of the picking process. Thanks to this, one order can be distributed in several containers, which speeds up the handling of large orders.
Singles Strategy
The Single strategy assumes that only one type of material can be in one container, but from many different orders. This approach facilitates precise control over products and minimizes the risk of errors. It is particularly useful in industries that require high precision, such as pharmaceuticals or electronics.
Picking trolleys
Picking trolleys are special carriers that transport containers in the warehouse. They are designed to facilitate quick and ergonomic order picking, increasing the efficiency of warehouse workers. The trolleys can be equipped with identification systems that facilitate the management of the picking process.
Courses
A route is the optimal route for a warehouse worker to move, generated by the WMS system based on the location of products. Each route can have only one picking strategy assigned (Mixed or Single), which ensures process consistency. Route optimization shortens the time employees spend moving and increases picking efficiency.
Packing station
The packing station is the last stage of the multi-picking process, where products go after completion of picking. Warehouse workers perform the final check of orders, pick them into appropriate packages and prepare them for shipping. Effective management of the packing station speeds up order fulfillment and improves the quality of customer service.
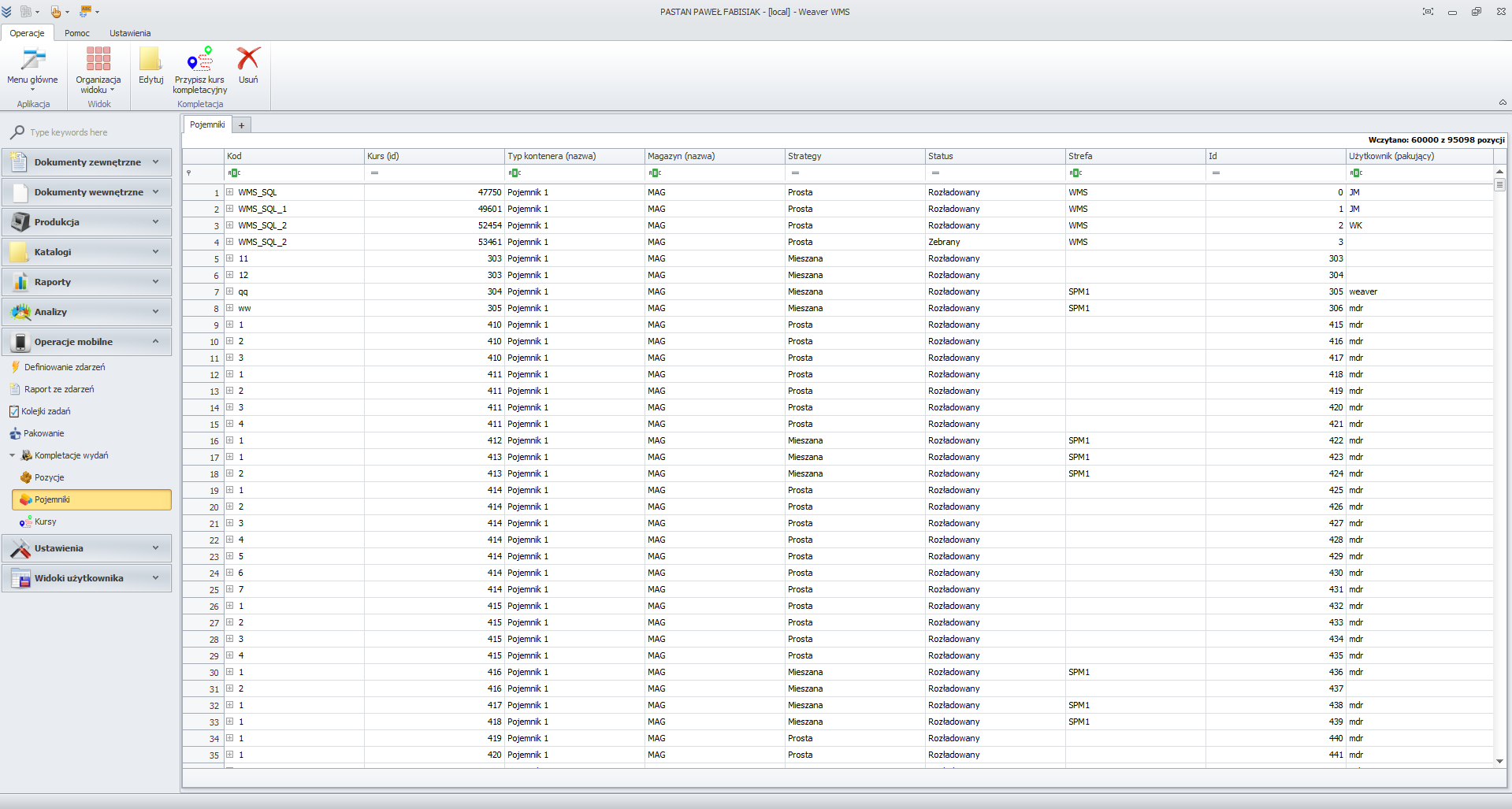

Multipicking is a technique used in warehouses that involves picking multiple orders at once, rather than picking each one individually. This minimizes the movement of the warehouse worker and speeds up the entire picking process. Orders are grouped according to specific criteria, such as product location or type, and the warehouse management system (WMS) optimizes the worker's route to reduce the time it takes to move around the warehouse. In the Weaver WMS, the multipicking process is based on different packaging strategies, bins and picking carts, and the final stage is the packing station, where orders are separated and prepared for shipping.
Test all system integrations and functions for 30 days
Without payment and providing payment details.