The Weaver WMS warehouse system supports quantitative warehouse management. What if the company is already serviced by a sales program and we want to be able to use information documents? All you need to do is implement our proprietary solution - Weaver WMS - which is fully compatible with sales and accounting programs.
What documents does the WMS system exchange with external systems such as ERP and accounting?
WMS systems are rarely implemented as autonomous solutions, disconnected from the rest of the company. Usually, WMS is integrated with at least one external solution and this is it ERP or accounting system (invoicing and accounting). Various scenarios will be discussed below document integration between systems. The scenarios presented below are basic scenarios, the integration process is often adjusted during implementation to the company's requirements.
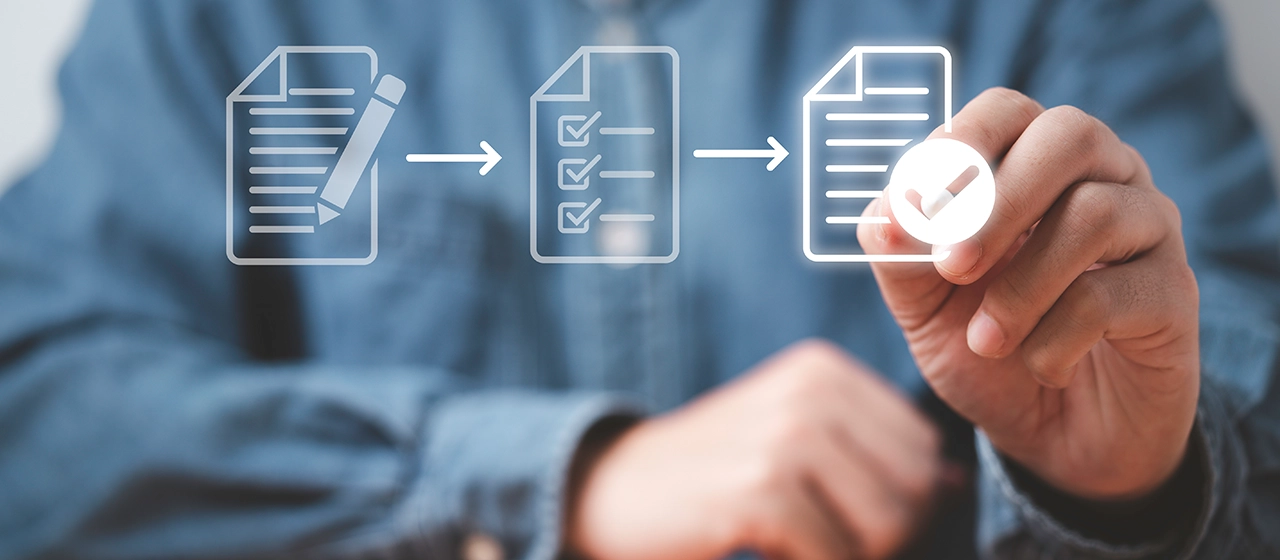
Did you know that...
- Did you know that the first ERP systems appeared in the 1960s? Initially, they were used mainly for planning production resources, and their development occurred as the complexity of business processes increased.
- Where does the name "Enterprise Resource Planning" come from? Well, this term was introduced in the 1990s. It was originally called MRP, i.e. Material Requirements Planning, but over time, aspects related to enterprise resource planning were added to it.
- Modern ERP systems consist of various functional modules, covering areas such as finance, human resources, production, sales, as well as customer relationship management (CRM). The interesting thing is that these modules are usually integrated, which allows you to effectively manage all aspects of your company's operations.
- In the era of digital transformation, ERP systems play a key role. They allow companies to modernize their business processes, improve data management and quickly adapt to changing market conditions.
- More and more companies are moving to cloud ERP solutions. Did you know that using an ERP system in the cloud can bring benefits such as easy access to data from anywhere, scalability and lower IT infrastructure costs?
- ERP systems are also known for the role they play in supporting decision-making processes. By collecting and analyzing data from various areas of the company, they provide company leaders with valuable information needed to make effective strategic decisions.
Inventory (physical inventory). This is where you should start.
Companies that do not have a WMS usually know how much of what they have (though not always), but they do not where do they have it and what is its expiry date, batch number, packaging, etc. Implementation you should start with a physical inventory in the WMS system of all warehouses warehouse management will be supported by WMS. It should be accurate to the place count all the goods in the warehouse.
The inventory documents created in WMS are sent to the system after its completion parent ERP/FK. Thanks to this, after the production launch of the systems, the states warehouses in the systems are consistent.
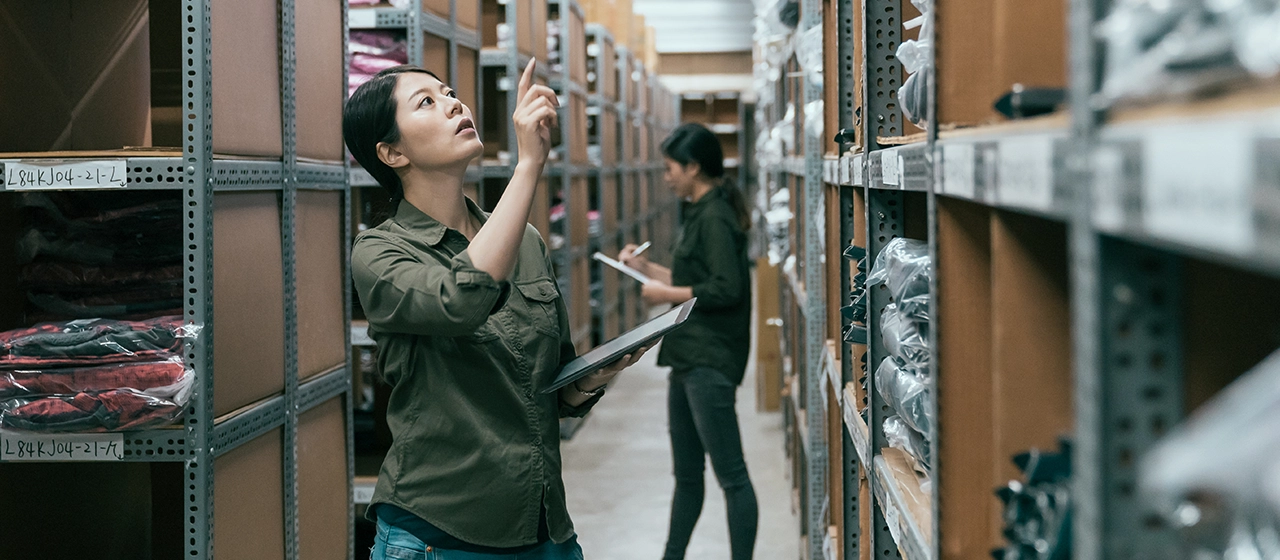
External receptions. Several roads.
Apart from issues, receipt is the most important document in warehouse systems. Doubts This does not apply to the fact that the receipt of goods must take place in the warehouse, using the system closest to you warehouse is a WMS system. Delivery, however, may be notified (scheduled) or adhoc (executed when the goods arrive, without prior notification).
- Delivery without notification - If the company carries out unnotified deliveries, they should be made in the system WMS. In short, it looks like this: the goods that have arrived at the company are checked qualitatively (we assume that the check was successful, with various scenarios for dealing with shortages, a separate entry will be created), we scan on the terminal mobile goods, we label them with logistic units (if they were not labeled) or codes of goods (if they were not labeled) and we accept them at the place of delivery (buffer) for subsequent transfer to the appropriate storage place. After the External Receipt document is approved in the WMS system, it is exported to the ERP/FK system as a PZ document, where it should be combined with the Purchase Invoice and sent value of goods in the ERP/FK system.
- Notified (planned) delivery - A more common scenario is delivery notification,
because the goods have to be ordered somewhere to be delivered
he came. It's a good idea to keep orders to suppliers in the system instead
only in the form of e-mail correspondence.
The notification can be added in the WMS system as an Order to the supplier, generate a PDF and send it to the supplier. Then, when the goods arrive, you can create a PZ document from the ZD document (Orders to the supplier) and check it in terms of quantity and quality. The system will mark any discrepancies on the document and they should be clarified with the supplier. The optimal scenario is to keep Orders to suppliers in the ERP/FK system and evaluate them at this stage. The integrator will download the order form to the WMS system (delivery notice). After receiving the goods in the WMS, similarly to the previous scenarios, the integrator will send the GRN document to the master ERP/FK system. This time, however, the integrator will additionally connect the GRN with the order in ERP / Invoice, thanks to which the GRN will have the values of the received goods entered.
External edition. What's most important.
This is undoubtedly the most important and most frequently occurring and integrated document in warehouse systems. It is rarely added manually to WMS, although this is of course possible. Usually, the notification of an External Issue in the form of a ZK (Order from a Customer) is downloaded from the ERP/FK system in question or it can be downloaded from another source (online store, Allegro, Baselinker system folder, etc.).
A very important element when downloading the ZK to WMS is the correct downloading and mapping of shipping data, such as the recipient's contact details, the courier company handling the delivery and any information about the cash on delivery payment. These data are often saved by companies in ERP in different ways, e.g. as a form of payment.
Once the ZK is in the system, it should be implemented as an External Issue document. I will not write about the scenarios of WZ implementation in WMS, there will certainly be a separate entry about it. The WZ document prepared in WMS must be sent to the ERP/FK system. If the ZK existed in ERP/FK, the integrator connects the WZ with this ZK. This is usually where the integrator's role ends, unless... there is a need to include a sales document (invoice, receipt) in the package. Then, an additional element is incorporated into the WZ implementation process in the WMS (after the goods are completed and before they are packed) in the form of issuing a sales document to the WZ in the master ERP/FK system and downloading it to the WMS system as an attachment to the WZ. Then, during packaging, such a document will be printed together with a courier label.
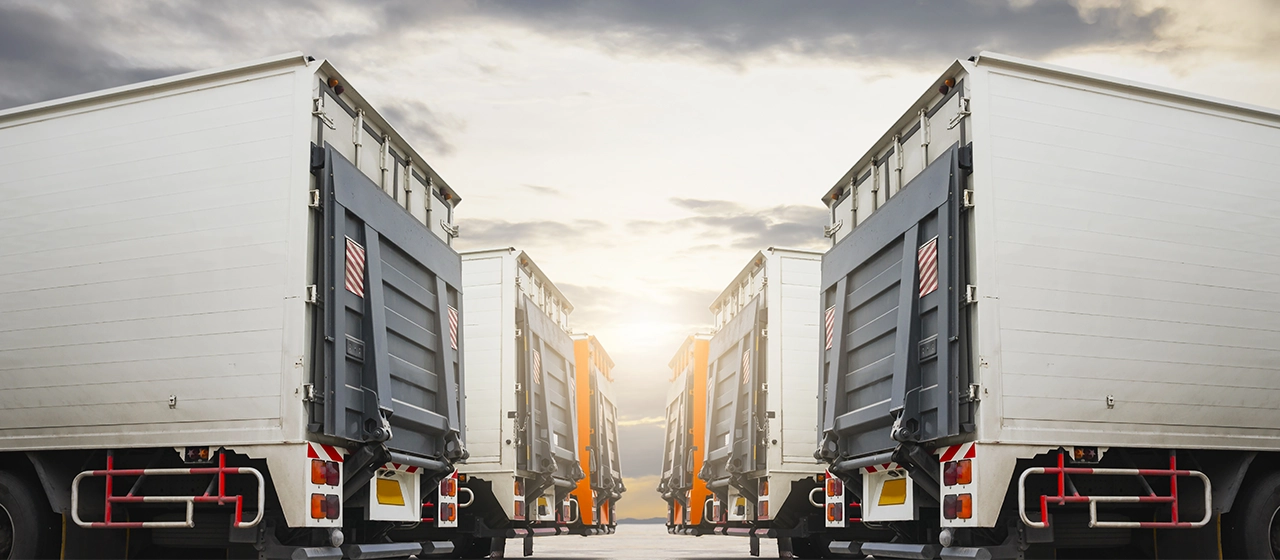
Internal revenues and expenses.
Internal Revenues and Expenditures are documents that are created in the WMS system as a result of warehouse operations. These are situations in which, in short, we create or liquidate something (losses, damages, miraculous discoveries, acceptance of a finished product from production, release of raw materials for production, disposal of packaging, etc.). Once created in the WMS, such an Internal Revenue or Expenditure document must be sent to the master ERP/FK system to the appropriate warehouse in order to maintain consistency of inventory levels.
Inter-warehouse transfers.
If in the WMS system we operate not only a warehouse of finished products, but also a warehouse of raw materials or a production warehouse, MM documents (Inter-warehouse transfer) should be integrated into the ERP/FK system. Such a document, like PW and IR, is created in WMS and sent to ERP / Invoice, moving the goods to the appropriate warehouse. There are also intra-warehouse transfer documents in the WMS, but these are not integrated because the ERP does not know anything about the location of the goods inside the warehouse.
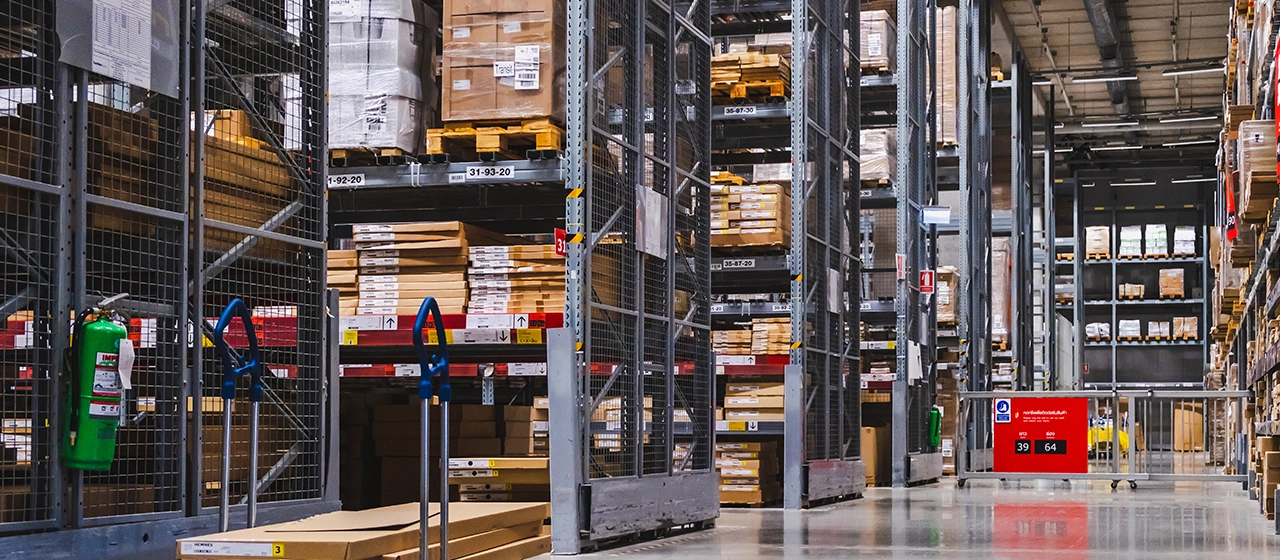
Materials. Suppliers. Recipients.
When synchronizing documents, the integrator also exchanges information about materials, suppliers and recipients. Usually, these entities are downloaded from the ERP/FK system to WMS, because it is a superior system and needs more information, e.g. tax information. Automatic creation of a commodity, supplier or customer card in ERP by an integrator is not particularly recommended unless you know what you are doing...
Other system entities.
Of course, you can integrate much more than just documents. For example, you can download inventory levels from the ERP system to the WMS and compare them using the inventory discrepancy report available in the WMS. Scenarios for the integration of Production Orders, Production Orders and many others are also available. Details are agreed during implementation.
From the technical side…
The service operating in a specific cycle is responsible for integration. The service connects to the database or API of the parent system. Information defined during configuration is exchanged in each cycle. Data is exchanged automatically. After the cycle ends, there is a short break and the next loop starts automatically. Thanks to this, information is exchanged between both systems in real time.
During integration, in a dedicated panel, it is possible to verify what exactly is happening in a given cycle. The client has access to the full history of each cycle's operation along with detailed logs.