Implementing a warehouse system is a key step in optimizing a company's logistics processes. Properly preparing the company for this task allows you to avoid problems, minimize the risk of errors and ensure efficient and effective warehouse operation. In this article, we will present what to pay attention to so that the implementation is successful and brings the expected benefits.
Preparing the IT infrastructure: The foundation for a new warehouse system
Before implementing a new warehouse system, it is crucial to ensure that the appropriate IT infrastructure is in place. It is important to ensure that the computer equipment, server, terminals and printers are compatible with the new software. It is also worth paying attention to the stability and speed of the internet connection, especially if the system is cloud-based. Data protection should be a priority, so it is worth implementing appropriate security measures and a regular backup plan to minimize the risk of data loss.
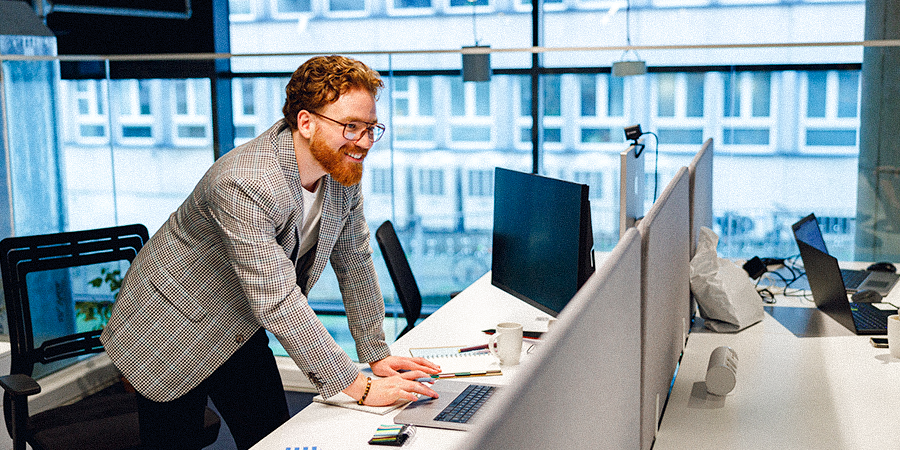
Discussing the implemented processes with staff: The key to effective adaptation
Communication with staff is key to implementing a new warehouse system. Employees should be fully informed about the upcoming changes and how they will affect their daily duties. It is worth organizing informational meetings and training sessions to explain the new procedures and answer any questions.
Hands-on training, such as simulations, can help to better understand and master new tools. Staff involvement at this stage increases the chances of successful implementation and minimizes the risk of operational errors.
Prepared warehouse – designated and marked storage locations: Order before implementation
In order for the implementation of the new warehouse system to proceed smoothly, it is important to properly prepare the warehouse space. It is necessary to precisely designate and mark the places where goods are stored and the work areas, which will facilitate orientation in the warehouse and speed up the logistics processes. Order and clear marking of storage places will allow for easier implementation of the new system and minimize potential problems related to the location of goods.
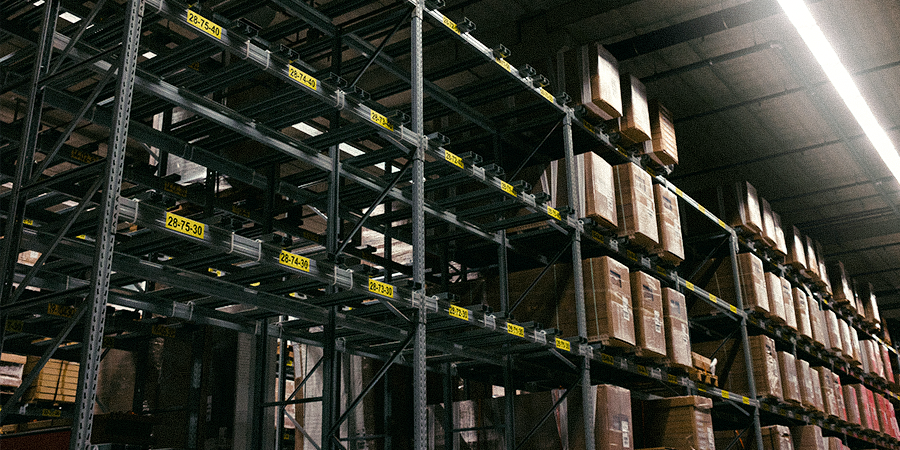
Barcoding Materials: The Key to Effective Inventory Management
If there are materials in the warehouse that are not yet marked with barcodes, it is worth taking care of their proper marking before implementing the system. Barcodes facilitate the tracking of goods, speed up warehouse processes and reduce the risk of errors when receiving and issuing goods. Thanks to barcodes, the warehouse system will be able to automatically identify products, which will increase operational efficiency and accuracy of inventory records.
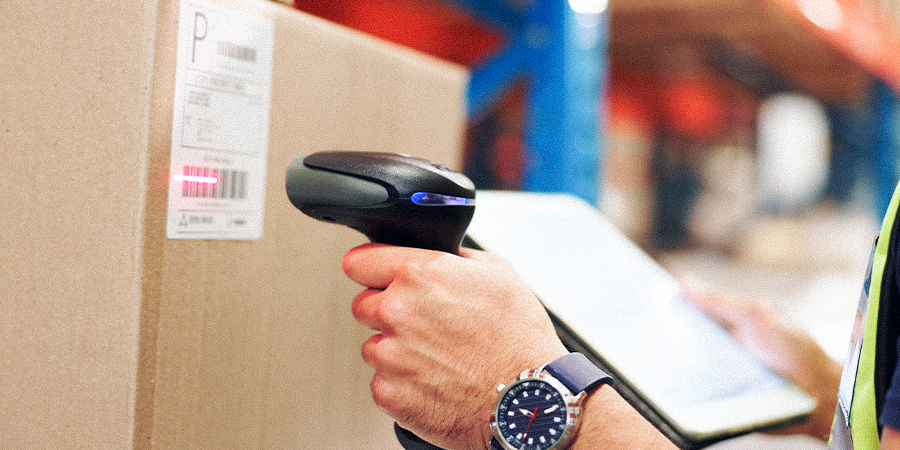
Taking an inventory: Updated data as a starting point
Inventory is a key step before implementing a new warehouse system. An accurate inventory taken just before or after implementation will allow for the updating of inventory data. This will ensure that the new system is based on current information, ensuring accurate and reliable inventory management from the start. Regular inventory after implementation will also help monitor the effectiveness of the new system and adjust it to the operational needs of the company.
Each of these points is a key element of preparations for the implementation of the warehouse system and should be carefully considered and appropriately addressed to ensure a smooth transition to the new system and maximization of the benefits from its implementation.