Implementation of the Weaver WMS system at Eurofrance.
Eurofrance is a dynamically developing company that has been selling car parts for years – both new and used. It specializes in supplying components for various car brands, offering its customers a wide range of high-quality spare parts.
Thanks to its experience and extensive network of suppliers, Eurofrance has gained the trust of individual and business customers in the automotive market. Due to the constantly growing demand and the need to maintain a high standard of service, the company decided to optimize its warehouse processes by implementing the Weaver WMS system.
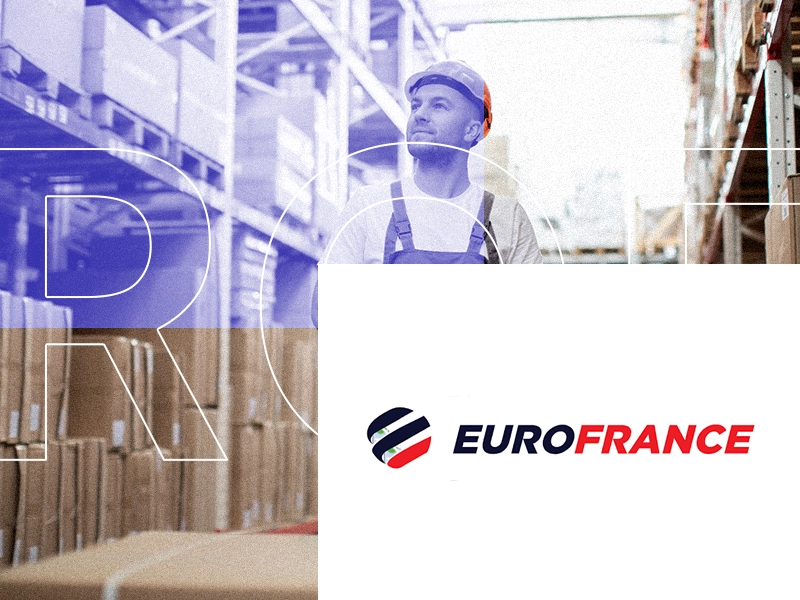
Project Objectives
In response to the dynamic development of its business and the growing demands of the market, Eurofrance decided to modernize its warehouse processes. The key task was to improve the handling of e-commerce orders that come from various sales platforms. Effective management of this process was aimed at accelerating order fulfillment while minimizing the risk of errors in picking goods.
An additional priority was to improve the identification of individual goods in the warehouse. The large variety of car parts required the implementation of precise location mechanisms and unambiguous product marking. The implementation of these goals was to provide the company with higher operational efficiency and even better customer service.
Solutions implemented by Weaver WMS
To meet the specific requirements of Eurofrance, the Weaver WMS implementation team used a number of advanced solutions that streamlined key warehouse processes. One of the key elements of the implementation was the integration of the WMS system with the company's ERP system – Subiekt GT. This solution enabled bidirectional data exchange, including warehouse documents, information on the assortment and the customer database. Thanks to this, all processes taking place in the warehouse were synchronized with the company's commercial and accounting activities, which significantly simplified the management of operations.
Another solution implemented was the identification of batches of goods based on photos. Each batch received unique photographic documentation, which not only allowed for easier searching for goods in the warehouse, but also for more efficient handling of returns and complaints. The introduction of this process reduced the number of errors related to issuing products and improved the transparency of operations.
In addition, the Weaver WMS system was integrated with the sales platforms used by Eurofrance. This integration ensured full automation in the scope of sending orders to the warehouse system and synchronization of fulfillment statuses. Moreover, photos of the goods batches entered in the WMS system were also available on the sales platforms, which increased the credibility of the offers and helped customers to choose products more precisely. These comprehensive solutions significantly improved warehouse operations and integrated them with the rest of the company's business processes.
Results and benefits
The implementation of the Weaver WMS system significantly improved warehouse processes and e-commerce order handling at Eurofrance. Automatic integration with sales platforms accelerated order fulfillment, eliminating errors, which resulted in greater customer satisfaction. Identification of goods using photos made it easier to locate products and handle complaints, increasing the transparency of operations.
Integration with Subiekt GT optimized the exchange of warehouse documents and inventory management, allowing for better adjustment of the offer to customer needs. Shortened order fulfillment time and automation of operations increased the efficiency of warehouse work, increasing the company's competitiveness on the market.
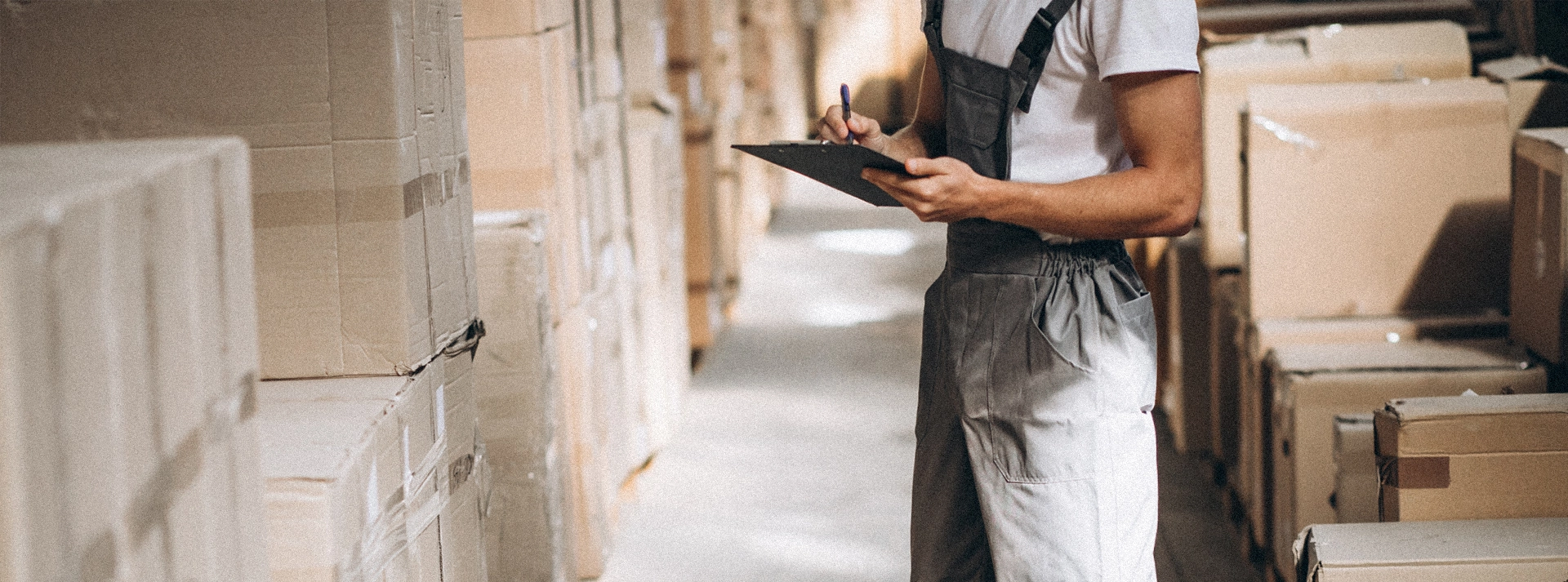
Summary
The implementation of Weaver WMS at Eurofrance was a breakthrough in the modernization of its warehouse and e-commerce operations. Thanks to precisely tailored solutions, such as integration with Subiekt GT and sales platforms, the company gained greater operational efficiency and better process synchronization. The introduction of goods identification based on photos not only reduced the number of errors, but also significantly improved the transparency and convenience of product management.
The implementation results exceeded expectations, ensuring faster order fulfillment, higher quality customer service and more efficient use of warehouse resources. Thanks to the implementation of the Weaver WMS system, Eurofrance can better respond to market needs, build a competitive advantage and develop based on modern technologies.
To meet the specific requirements of Eurofrance, the Weaver WMS implementation team used a number of advanced solutions that streamlined key warehouse processes. One of the key elements of the implementation was the integration of the WMS system with the company's ERP system – Subiekt GT. This solution enabled bidirectional data exchange, including warehouse documents, information on the assortment and the customer database. Thanks to this, all processes taking place in the warehouse were synchronized with the company's commercial and accounting activities, which significantly simplified the management of operations.