System implementation at FlexLS.
Flexible Logistics Services Sp. z o.o. is a dynamic fulfillment service provider specializing in comprehensive logistics services for clients with diverse storage needs. It serves clients who have a variety of goods, from small-sized products, through non-standard-sized goods, to products with special storage requirements.
In its operations, the company focuses on providing the highest quality services, including receiving, storing, completing orders and shipping. Due to the growing demand from customers for fast and precise warehouse operations and the increasing number of orders handled, Flexible Logistics Services Sp. z o.o. decided to implement the modern Weaver WMS warehouse system. The goal was to streamline processes, improve operational efficiency and adapt to the requirements of the dynamic fulfillment services market.
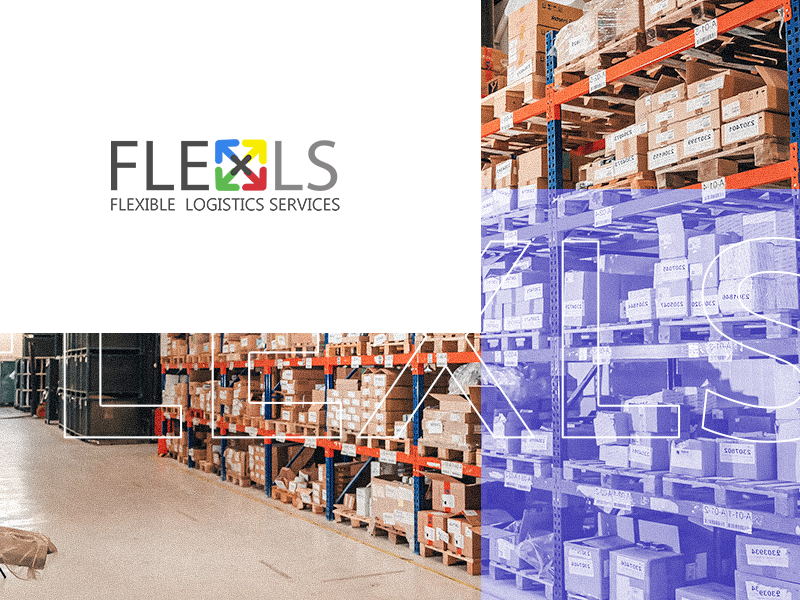
Project Objectives
The company set ambitious goals for the implementation of the Weaver WMS system, aimed at streamlining and automating warehouse processes to meet growing customer demands. Key project goals included:
Accurate tracking of goods in the warehouse
Due to the diverse nature of goods stored in the warehouse, one of the main goals was to introduce precise tracking of each product. The company aimed to achieve full traceability of goods, from the moment they were received in the warehouse to their shipment to customers. The Weaver WMS system was to enable easy tracking of product locations, batches, serial numbers and expiration dates, which is crucial to maintaining high quality of services.
Speeding up order fulfillment
Due to the rapidly growing number of orders, the goal was to significantly shorten the order fulfillment time. The company wanted to streamline the picking and packaging process to process orders faster and more efficiently, while reducing the risk of errors. By automating and optimizing warehouse processes, Flexible Logistics Services Sp. z o.o. intended to raise the standard of service, providing customers with fast and reliable delivery.
Increasing the scale of operations
As the number of customers and the variety of products served increased, the company set itself the goal of increasing the scale of its operations. The implementation of the Weaver WMS system was to enable effective management of a larger number of goods and orders without the need for a proportional increase in human resources. The goal was to create a flexible and scalable warehouse system that would allow for quick adaptation to changing market conditions and business growth.
Solutions implemented by Weaver WMS
During the implementation of the Weaver WMS system at Flexible Logistics Services Sp. z o.o., a number of advanced solutions were introduced that significantly improved and automated warehouse operations:
Multi-picking
The system has launched a multi-picking process that allows for the simultaneous completion of multiple orders in a single picking cycle. Thanks to this solution, warehouse workers can collect products for several orders in a single attempt, which has significantly shortened the lead time and reduced the number of kilometers traveled in the warehouse. Multi-picking has optimized the picking process, increasing efficiency and reducing the workload of staff.
Automatic optimization of goods in the warehouse
The Weaver WMS system introduced the ability to automatically generate warehouse transfers based on current orders and forecasted demand. This feature allowed the company to better utilize warehouse space and speed up picking processes.
Tracking product expiration dates
In the case of storing diverse goods, including products with a specific expiration date, implementing precise tracking of expiration dates was crucial. Weaver WMS enabled precise management of batches of goods and their expiration dates, which allowed for effective inventory management and prevention of product expiration. The system automatically identified goods with the shortest expiration date, prioritizing them in the picking process. It also ensured that products with too short an expiration date were not sent to customers.
Synchronization of completed orders with the Way2Send system
One of the important elements of the implementation was the connection of the Weaver WMS system with the Way2Send platform. Thanks to this integration, after completing orders, information was automatically transferred to the shipping system, which accelerated the shipping process and minimized the risk of errors.
The introduction of these solutions through the Weaver WMS system allowed the company to significantly streamline its warehouse operations, increase efficiency and improve the quality of services provided, while meeting the growing demands of its customers.
Results and benefits
Implementation of the Weaver WMS system at Flexible Logistics Services Sp. z o.o. brought a number of significant benefits. First of all, thanks to multipicking and automatic optimization of goods, it was possible to increase operational efficiency, which translated into faster order fulfillment and cost reduction. The system also enabled precise tracking of goods and inventory management, eliminating errors related to product expiration and improving the overall quality of service. Integration with the Way2Send system allowed for more efficient order shipping, which increased customer satisfaction. In addition, the implementation of Weaver WMS allowed the company to increase the scale of its operations without the need to significantly increase resources. Thanks to this, the company could effectively handle a larger number of orders while maintaining the high quality of services provided.
Summary
The implementation of the Weaver system turned out to be a strategic step that significantly improved and automated warehouse operations. Thanks to advanced functions, the company achieved significant acceleration and improvement of order fulfillment.
Weaver WMS also provided tools for ongoing monitoring and analysis of warehouse performance, which allowed for more informed operational and strategic decisions. This implementation contributed to strengthening the position of Flexible Logistics Services Sp. z o.o. in the fulfillment services market, raising service standards and enabling dynamic development in response to growing customer needs.
In summary, Weaver WMS has become an integral part of the company’s warehouse operations, providing the company with a competitive advantage and enabling it to deliver the highest level of service.