Implementation of the Weaver WMS system at Kaps.
The company for which the Weaver WMS system was implemented is a renowned manufacturer specializing in the creation of care and protective products for footwear, as well as shoe inserts. This brand has been building its position on the market for years, providing products that combine high quality with innovative solutions. The company's assortment includes a wide range of products, from shoe cleaning and maintenance products to specialist inserts that provide comfort and protection for the feet.
Dynamic development and constantly growing demand for products meant that the company had to face the need to improve warehouse management. The key element of the business was the need to optimize logistics processes to meet market requirements and at the same time maintain the highest quality of customer service. The company decided to implement a modern warehouse system Weaver WMS, which allows for process automation and full control over warehouse stock.
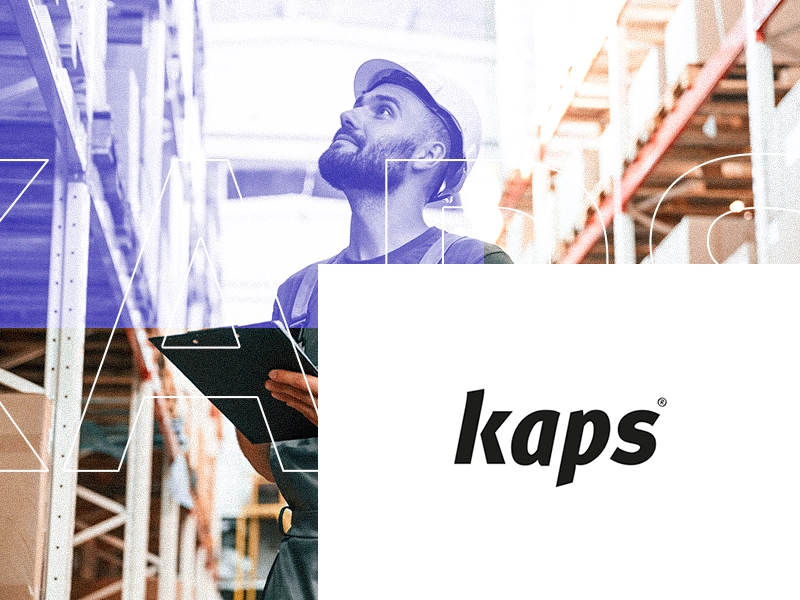
Project Objectives
The aim of implementing the Weaver WMS warehouse system at Kaps Sp. z o.o. was to adapt warehouse processes to the dynamically developing business and growing customer needs. The company wanted to gain a modern tool that would not only streamline daily work, but also allow for effective management of the entire logistics chain.
One of the priorities was to ensure full transparency and the ability to track the movement of goods in the warehouse - from the moment of receipt, through production processes, to the release of the finished product. Thanks to this, the company intended to minimize errors, improve the accuracy of warehouse stocks and streamline inventory management.
An equally important goal was to optimize e-commerce store service, which is an increasingly large part of the company's operations. Automation of order picking and shipping processes was to contribute to faster order fulfillment and increased satisfaction of retail and wholesale customers.
In addition, the system was to support the handling of production processes through smooth management of the flow of raw materials and components between production and the warehouse. The use of Weaver WMS was to enable better synchronization between departments and ensure more efficient execution of production orders. In this way, Kaps Sp. z o.o. could increase the efficiency of its operations and maintain a competitive advantage on the market.
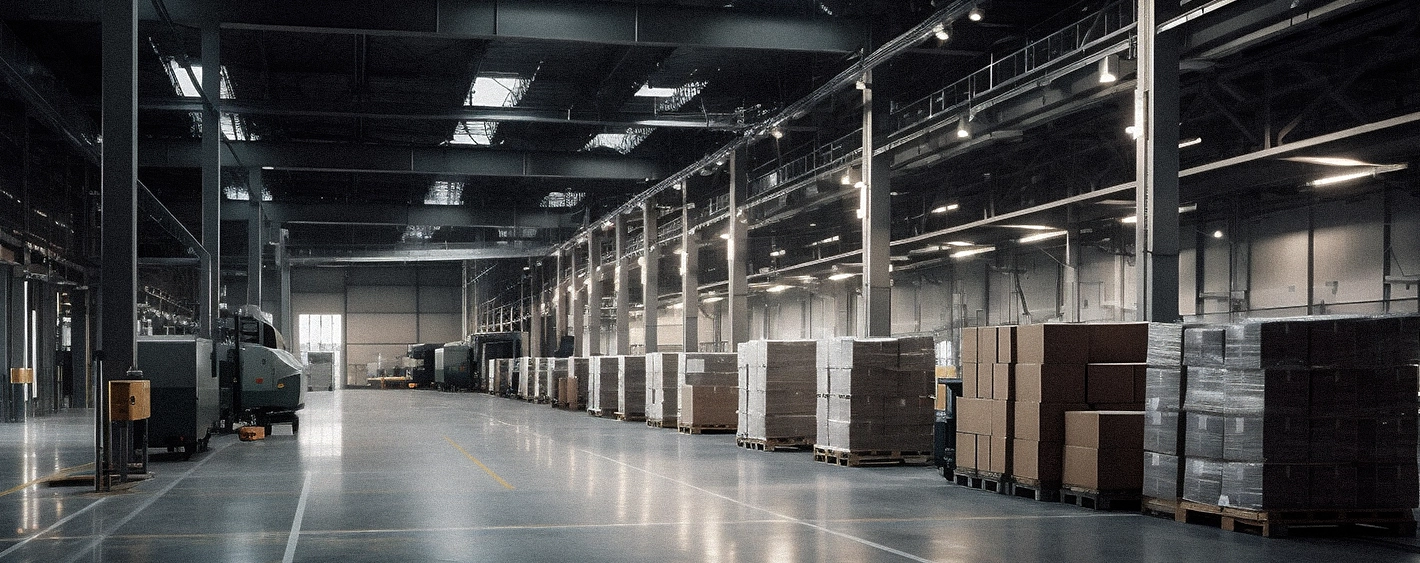
Solutions implemented by Weaver WMS
The implementation of the Weaver WMS system at Kaps Sp. z o.o. included a number of innovative solutions that were precisely tailored to the specifics of the business and the needs of the client. Each of them was aimed at optimizing key warehouse, production and sales processes, which contributed to increasing the company's operational efficiency.
The first important step was to optimize the handling of orders from e-commerce panels. The WMS system was integrated with sales platforms, which allowed for automatic transmission of orders and their processing in the warehouse. The intuitive process of collecting goods, supported by additional integrations with transport companies, significantly shortened the order fulfillment time, improving the quality of customer service and increasing warehouse throughput.
The next step was to implement full support for production processes and kit completion. Thanks to this solution, the company could easily manage the flow of raw materials, control production stages and create ready-made product sets. Automation of these activities ensured smooth operations and minimized downtime.
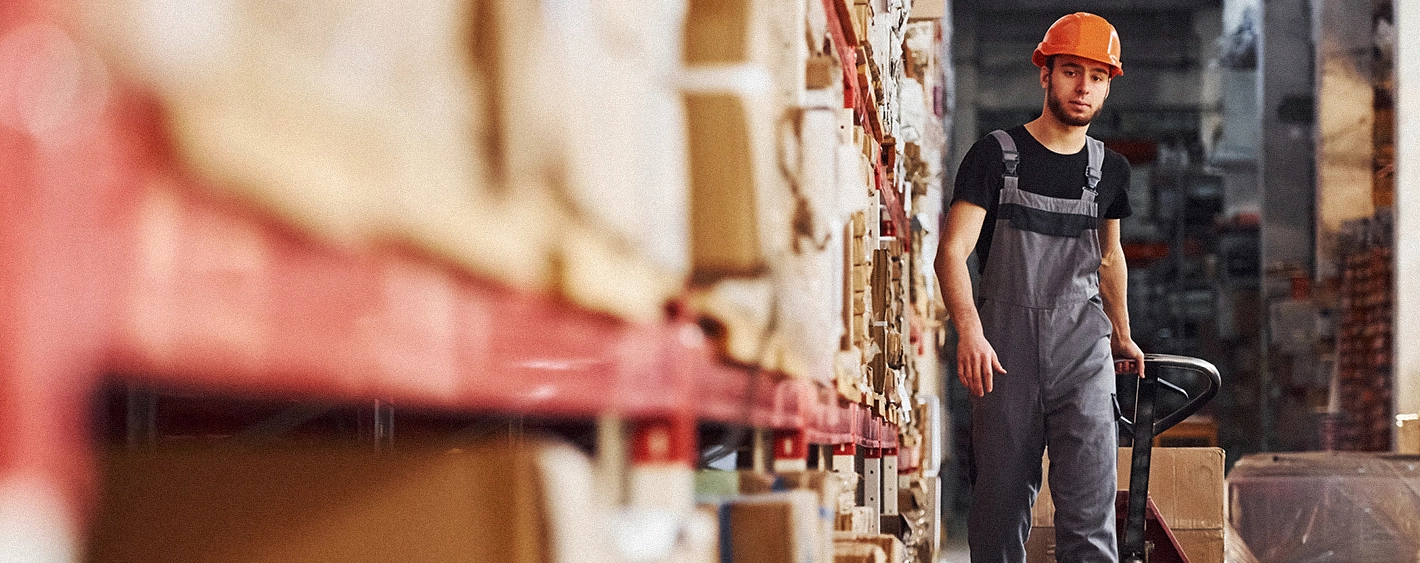
Weaver WMS has also been enriched with a proprietary B2B panel, which has been integrated with the warehouse system. This tool allows wholesale customers to place orders directly through an intuitive interface, which not only increased the convenience of cooperation, but also automated the handling of wholesale orders, eliminating the need for manual data processing.
The last key element of the implementation was the integration of the Weaver WMS system with ERP Enova. This enabled full synchronization of warehouse documents and invoices, which significantly improved the flow of information between systems and enabled better management of finances and warehouse stocks.
These comprehensive solutions allowed Kaps Sp. z o.o. to optimize its processes, increase efficiency and improve service to retail and wholesale customers.
Results and benefits
The implementation of the Weaver WMS system significantly improved the operations of Kaps Sp. z o.o., bringing tangible results in key areas of activity. Automated handling of e-commerce orders and warehouse processes allowed for shortening the order fulfillment time, improving the accuracy of picking and increasing customer satisfaction.
Integration with the Enova ERP system and implementation of the B2B panel contributed to better documentation synchronization, simplified sales processes and improved inventory management. Support for production processes and kit completion, in turn, increased operational fluidity and enabled more efficient use of resources.
Thanks to the solutions applied, the company gained higher efficiency, better control over logistics processes and greater flexibility in responding to market needs, which strengthened its competitive position.
Summary
The implementation of the Weaver WMS system at Kaps Sp. z o.o. included a number of innovative solutions that were precisely tailored to the specifics of the business and the needs of the client. Each of them was aimed at optimizing key warehouse, production and sales processes, which contributed to increasing the company's operational efficiency.
The results of the implementation were felt almost immediately – order fulfillment times were shortened, the precision of warehouse operations was increased and the quality of customer service was improved. Moreover, the improvements introduced allowed for better use of resources and a reduction in costs related to storage and logistics.
The Weaver WMS system has proven to be a key element of the company's development strategy, providing greater flexibility in responding to changing market needs and supporting business scalability. Thanks to this implementation, Kaps Sp. z o.o. is prepared for further development and increasing its competitiveness on the domestic and international market.