System implementation at Pajor.
Pajor Technology Sp. z o.o. is a dynamically developing company specializing in the production of high-quality mechanical parts. Operating on the domestic market, Pajor Technology has gained a reputation as a reliable supplier that focuses on precision of workmanship, innovative technologies and care for meeting the highest quality standards.
In response to the growing demands related to logistics management and warehouse processes, the company decided to implement a modern warehouse management system (WMS). The implementation was aimed at streamlining warehouse operations and ensuring full control over the flow of goods and materials in the warehouse.
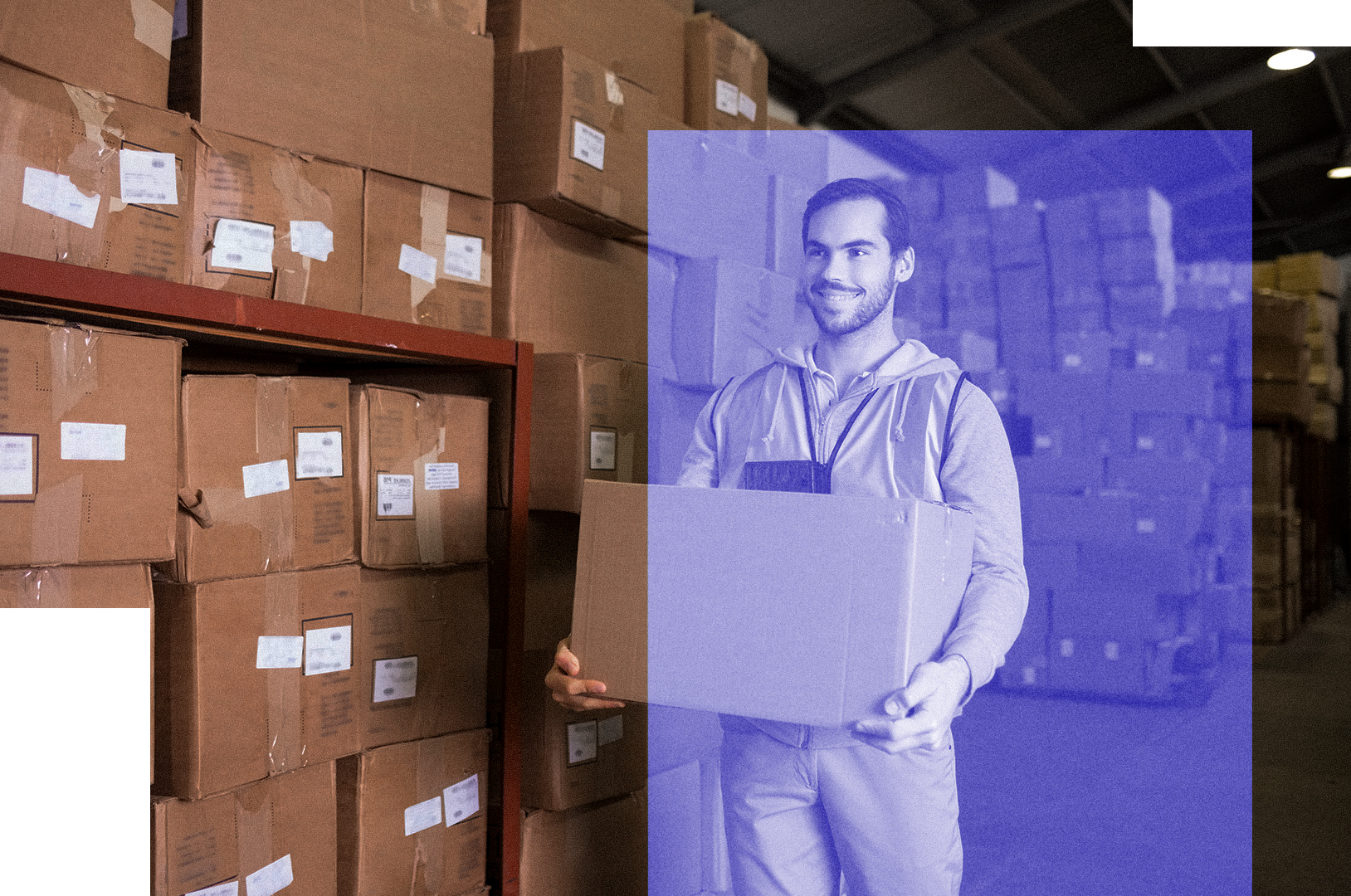
Project Objectives
The main objective of the Weaver WMS implementation project at Pajor Technology Sp. z o.o. was to streamline and automate the management of warehouse and production processes, which was to directly translate into increased operational efficiency and cost optimization. The key task was to create a coherent and integrated environment that would enable full control over the flow of materials and goods from the moment of receipt at the warehouse, through production processes, to final shipment to the customer.
To achieve these goals, the implementation project focused on several key areas.
Grouping orders by projects
At Pajor Technology, each production and warehouse order is linked to a specific project. The implementation of the Weaver WMS system was intended to facilitate the management of these orders, enabling their effective grouping, monitoring and settlement in the context of individual projects. Thanks to this, the company can more easily track the progress of work, allocate resources and control costs at the level of each project.
Obsługa procesów magazynowych
Celem było zapewnienie pełnej automatyzacji i optymalizacji procesów magazynowych, w tym przyjmowania, składowania, kompletacji i wysyłki towarów. System miał również zapewnić dokładne śledzenie stanu zapasów oraz lokalizacji każdego elementu w magazynie, co jest kluczowe dla utrzymania wysokiej jakości obsługi oraz terminowości dostaw.
Production process support
The implementation of the WMS system was also aimed at streamlining production processes by optimizing the management of materials and components used in production. The Weaver WMS system enables better synchronization between the warehouse and production, which contributes to the elimination of downtime and more efficient use of resources.
Integration with the ERP system "Subiekt Nexo"
The key element of the project was the integration of Weaver WMS with the company's existing ERP system "Subiekt Nexo". This integration enabled automatic data exchange between the systems, which allows for consistent management of orders, stocks, invoices and financial data. Thanks to this, the company gained a comprehensive tool for managing all operations, which significantly increased transparency and control over business processes.
Summary
The implementation of the Weaver WMS system at Pajor Technology Sp. z o.o. proved to be a key step in the operational development of the company, bringing numerous benefits in both the short and long term. Thanks to a carefully planned and conducted implementation process, the company achieved significant improvement in the efficiency of its warehouse and production processes.
Increased operational efficiency
The implementation of the Weaver WMS system allowed for the automation of many manual processes, which significantly reduced the time needed to perform warehouse and production tasks. Employees gained a tool that facilitates everyday work, which translated into increased productivity and better use of available resources.
Better control over inventory levels
Thanks to precise tracking of stocks and the location of goods in the warehouse, Pajor Technology has gained full control over its stock levels. The system has enabled ongoing monitoring of the availability of materials, which is crucial for ensuring continuity of production and timely deliveries to customers.
Optimization of production processes
Integration of the WMS system with production processes enabled better management of materials and components used in production. Downtime related to the lack of available materials was reduced, which allowed for more smooth and efficient execution of production orders.
Integration with the Subiekt Nexo system
A key success was also the full integration of Weaver WMS with the ERP system "Subiekt Nexo". Thanks to this, the company can manage all key business processes from one, coherent system, which increased transparency and facilitated decision-making based on current data.
Improving quality and reducing errors
Process automation and data centralization in one system have contributed to a significant reduction in human errors that could previously occur in manual warehouse management. The system ensures that all operations are carried out in accordance with established procedures, which improves the quality of service and minimizes the risk of errors.
Better project management
Thanks to the function of grouping orders by projects, Pajor Technology gained greater transparency in order management. This allowed for more accurate monitoring of costs and progress of works in the context of individual projects, which facilitated resource management and planning of future activities.
The implementation of the Weaver WMS system at Pajor Technology Sp. z o.o. is an example of a successful project that brought tangible benefits to the company. Thanks to this system, Pajor Technology can now better manage its resources, respond to customer needs faster and more effectively achieve its business goals. Investment in modern technological solutions has proven to be a key element in further development and strengthening the company's position on the market.
Test all system integrations and functions for 30 days
Without payment and providing payment details.