Implementation of the Weaver WMS system at Hermespol.
Hermespol operates in many countries around the world. It focuses its operations mainly on the industrial and construction markets. The customer's demand was to automate warehouse processes in a newly built, modern hall in Kleszczewo near Poznań.
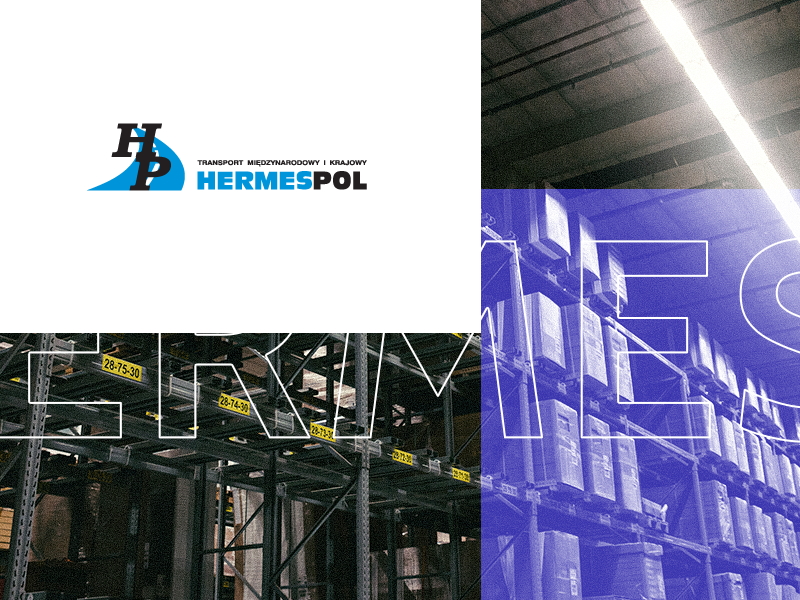
Customer requirements analysis.
The implementation was preceded by a thorough analysis of the customer's needs in terms of the warehouse system. It was determined that the goods would be issued from the warehouse on the FEFO (First Expire, First Out) basis, and the goods with the oldest expiration date would be the first to leave the warehouse. The batch numbers that are sent to customers are also important. The system must accurately track the batch numbers in order to accurately locate the faulty delivery in the event of a complaint.
The client's company also conducts accurate packaging management, and accurate information is required in terms of quantity regarding pallets. Information should be tracked about which supplier delivers which pallets, which recipient receives how many pallets.
An important requirement for the implemented system was also the possibility of advanced reporting on warehouse occupancy (number of occupied pallet spaces) in terms of regular materials and hazardous materials.
Due to the need to eliminate errors during the issuance of goods, the system was required to be able to conduct a so-called continuous inventory. When removing goods from a logistic unit, the warehouseman is obliged to enter the amount of goods remaining on the unit.
Network infrastructure and equipment.
Weaver Software initially prepared the network infrastructure at the customer's facility. This involved installing four wireless access points (two for each hall) and connecting them to the customer's existing network infrastructure. Two Motorola wireless data collectors, model MC32, and one TSC ME240 industrial label printer were ordered.
Installing the management application and importing data.
The next step of the implementation was to install the Weaver WMS PRO system on the client server and management applications on warehouse computers and at the management staff (for reporting purposes). The existing material catalog was imported from the Symfonia system, which saved a lot of time and eliminated the risk of errors during possible manual data entry. User accounts were created and system performance tests were conducted.
Marking the warehouse.
The client's facility consists of two warehouses. Weaver Software employees have marked the storage locations in each warehouse. Thanks to this, the warehouseman scans the code when putting the goods in the right place. This eliminates the risk of mistakes related to incorrectly putting the goods in the warehouse. Additionally, during the marking of the warehouse, the receiving and issuing buffers were separated.
The latest mobile technologies.
Most WMS systems available in Poland are equipped with outdated mobile applications based on Windows Mobile or Windows CE. Weaver WMS PRO is equipped with the latest mobile application working on the Android family system. The application is very efficient and high-contrast, making working with it a pleasure. The mobile version can be installed on almost any device equipped with the Android system, including a smartphone or tablet.
Receipt of goods.
The goods receipt process starts in the Weaver WMS PRO management application by creating a PZ document (External Receipt). Receipt items receive the 'New' status, each item added in the management application is of the 'Notified' type, which means it is planned. The warehouseman can create unplanned items on the data collector (when, for example, the supplier sends more items), such items are of the 'Ad-hoc' type.
Warehouse operations.
The system enables operations on logistic units. Operations can be forced by the system (e.g. optimization of the storage location of goods, shifts in relation to turnover indicators) and performed at the initiative of the warehouseman (e.g. when he notices the need to move goods due to internal conditions).
The basic information performed on logistic units is the preview of information about a given unit. After reading the unit code, information such as the name of the material, quantity, location, packaging, owner, weight, possible blocking, information about the nature of the material (whether it is hazardous) is displayed. Similarly, information about the batch of goods can be read (this can also be edited), such as the batch number, batch description, date of receipt, production date, expiration date. The system has implemented algorithms that calculate the expiration date depending on the type of assortment and production date.
By scanning the location code, you can view all units, along with basic information about them, located in a given storage location. Functions are also available to move, combine, separate and correct logistic units.
Inventory.
In addition to the continuous inventory process, which takes place in the system round the clock, during shipments, it is possible to plan and conduct a traditional inventory. In the Weaver WMS PRO management application, using the inventory opening wizard, it is possible to select places and materials that the inventory will concern. After planning the inventory, it is displayed on data collectors. Warehouse employees perform the inventory process by scanning the codes of logistic units, places and entering the actual quantity. When they finish their work, the inventory can be posted (quantity changes can be introduced) and closed (moved to the archive).
Issue of goods.
The goods issue process begins with adding a WZ (External Issue) document in the Weaver WMS management application. The company employee enters the appropriate quantities and selects the recipient. They can also set a planned issue date. The system continuously monitors the entered quantities for availability and displays appropriate messages in the event of a lack of goods in the warehouse. However, this is not an obstacle to adding the document, after all, the shipment can be scheduled for a later date, after the delivery of the goods.
After adding the document in the management application, the documents will be displayed to the warehouse worker in the data collector. When selecting a document, the warehouse worker will see a list of document items. The list shows the material (its code and name), the planned quantity and the quantity issued so far. Before starting the goods issue process, you can select the packaging used for issue (e.g. Euro pallet), then the system will include it in the issue document and create packing lists for individual packages.
When issuing goods, the system suggests material collection points and logistic units with the oldest expiration date (in accordance with the FEFO mechanism selected by Hermespol). In case of an error, the operation can be undone. Additionally, after picking the goods from the unit, the system will ask you to enter the quantity of goods remaining in the given storage unit (continuous inventory).
It is also possible to perform an optimized release (for one or more shipping documents at the same time). The system will then optimise the goods collection route so as to collect the appropriate goods in the most efficient manner.
Benefits of implementing Weaver WMS
Continuous inventory. During the shipment, warehouse workers must enter the remaining quantity left in the logistic unit after taking the goods from it. The system provides a report from the continuous inventory, which shows any discrepancies and release documents that may be incorrectly executed. This almost completely eliminates the risk of errors during shipment execution.
Report on pallet occupancy in the warehouse. A detailed report on the occupancy of pallet locations in the warehouse is very important information for the customer. The detailed report is available in the Weaver WMS PRO management application.
Report on stock levels and batches for a given day back. Thanks to the implementation of the Weaver WMS PRO warehouse system, it is possible to check the stock level for any day and hour back. Stock levels, batches, locations and many other useful information are shown.
Management of goods expiry dates. When entering a delivery, it is possible to enter the expiry dates of goods directly or enter the production dates of materials, the expiry dates will then be calculated automatically.
Report on operations performed during the receipt and issue of goods. For Hermespol, reports on the number of warehouse operations performed during the receipt and issue of goods are of great importance. The system meticulously counts each full-pallet operation (handling) and so-called pallet additions. Each operation is reflected in the report.